تولید لوله 6 اینچ فولادی به روش پوش بنچ
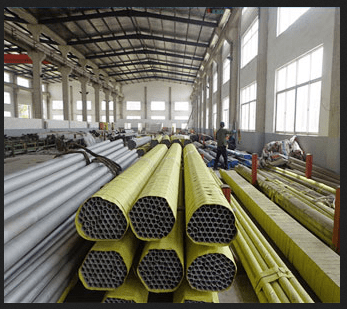
تولید لوله 6 اینچ فولادی به روش پوش بنچ
مقدمه
تولید لوله به طور کلی به دو روش عمده صورت میگیرد که عبارتند از درزجوش و بدون درز لوله درز جوش با شکل دادن سرد وق و سپس جوشکاری اولیه ورق توسط روشهای فرکانس بالا ، زیر پودری و غیره تولید میگردد
لوله بیدرز با استفاده از بلوم یا استانه فولادی به ابعاد مختلف و عملیات سوراخکاری و کششی گرم تولید میشود که بدلیل عدم وجود منطقه جوش و تنهشهای پسماند از همگنی بهتری در ساختار لوله برخوردار است که این امر باعث مقاومت بهتر لوله در برابر خوردگی ، محیطهای با شرایط حاد و غیره میگردد
فرایند تولید لوله خام بیدرز به روش میز شلیک ( پوش بنچ)
- مواد خام
- برش مواد
- عملیات سوراخ کاری
مواد خام
برای تولید این نوع لوله از بلوم فولادی مقطع مربع شکل به اندازه 200 * 200 میلیمتر اتفاده میشود گرید فولادی از فولادهای معمولی ساختمانی تا فولاد های کم آلیاژ و میکرئ آلیاژ می باشد .
برش مواد
در این مرحله بلوم ها بر روی یک اجاق قرار میگیرند و حدود 200 – 150 درجه سانتی گراد گرم میشوند و سپس توسط دستکاه قیچی گوتینی دوازده ای بطول مورد نظر بریده میشوند به این برش ها بیلت اطلاق میگردد .
عملیات پیشگرم و همگن سازی
بیلتهای بریده شده توسط ماشین شارژ مغناطیس وارد یک کوره پیش گرم از نوع کفگرد میشوند در این کوره بیلتهای فولادی به دمای 1300 درجه سانتی گراد رسیده و ساختار ریخته گری آنها همگن می شود کوره دارای 4 منطقه حرارتی با دماهای به ترتیب 1150 و 1250 و 1310 و 1300 می باشد که با عبور بیلت ها از مناطق حرارتی فوق ، ساختار ریخته گری انها همگن شده و در آخرین منطقه به دمای 1300 رسیده و اماده بهره برداری برای عملیات کارگرم میگردد
عملیات سوراخ کاری
پس از رسیدن دمای بیلت هابه 1300 از طریق روله ها انتقال بسمت دستگاه پرس سوراخ هدایت میشود
لازم ذکر است قبل از عملیات سوراخکاری پوسته های اکسیدی توسط غلتکهای پخ زن و فشار آب 150 باری پاک میشود . در این مرحله بیلت توسط پرس مطابق شکل یک سوراخ میشود اصولا سوراخکاری به دو روش انجام می شود در روش اول که غالبا از بیلت با مقطع مربع استفاده میگردد عمده تغییر شکل در هنگام سوراخکاری بصورت پر کردن فضای خالی بین بیلت و قالب است و در روش دوم بیلت بصورت یک استوانه می باشد و تقریبا تمام تغییر شکل صرف افزایش طول بیلت میگردد رابطه بین نیروپرس و نسبت قطر سنبه به قطر داخلی حوضچه در شکل (2) نشان داده شده است لازم بذکراست در تولید لوله 1.6 اینچ فرایند سوراخکاری ترکیبی از هر دو روش است بقسمی که مقداری از فرایند سوخکاری پرکننده و بقیه آن همراه با افزایش طول است طراحی قطر سنبه سوراخ کننده با توجه به شکل شماره 2 به نحوی صورت پذیرفت که نیرو و فشار پرس در محدوده مجاز قرار گرفت . در اثر این عملیات بیلت به یک شکل شبیه لیوان (Loppe)
تبدیل میگردد
ازدیاد طول لوپه
بعد از عملیات سوراخکاری لوپه توسط روله های انتقال بسمت دستگاه النگاتور هدایت میشود . در این مرحله ازنورد که به ASSEL MILL نیز معروف است قطر لوهپه کم شده و طول آن افزایش می یابد که همراه با کاهش ضخامت اختلاف ضخامت تولید شده در پرس نیز اصلاح میگرد شکل (3)
میز شلنگ
در این مرحله که مهمترین نورد لوله محسوب میشود ، لوپه خروجی النگاتور توسط یک عدد سنبه به داخل یکسری قفسه های سه غلتکی با کالیبرهای مختلف ( از بزرگ تا کوچک) شلیک میگردد ، نیروی شلیک توسط دو عدد موتور DC با توان حدود 2MW تامین میشود
در شکل زیر محصول خارج شده از قفسه های سه غلتکی یک پوسته بلند کشیده شده بر روی سنبه می باشد که طول این پوسته بین 8 الی 14 متر می باشد
- پوسته
- قفسه های غلطک
- سنبه شلیک
- شافت شلیک
- اسبک (نگهدارنده شافت
- تریلی رک
آزاد سازی لوله خام از سنبه و برش ضایعات
در این مرحله باید سنبه از لوله جدا گردد که اینکار توسط دو دستگاه شل کن و سنبه کش انجام میشود و سپس توسط اره های گرم بر ضایعات سروته لوله بریده میشود
مرحله دوم ( تولید نهایی )
کوره پیش گرم
لوله ها خام تولید شده بعد از برش ضایعات سروته وارد کوره پیش گرم میشوند این کوره از نوع گامی است با حرکت گامی لوله ها را به جلو برده و تا 960 درجه سانتی گراد دمای آنها را بالا میبرد
نورد SRM
لوله ها بعد از خرئوج از کوره توسط آببا فار بار اکسید زدائی و سپس وارد دستگاه کشش SRM میگردند – نورد SRM یک نورد پیوسته با حداکثر
قفسه سه غلتکی محرک می باشد شکل پایین در نورد SRM قطر و ضخامت نهایی لوله توسط چیدمان قفسه های سه غلتکی و ایجاد سرعتهای مناسب در موتور D بوجود می اید
بستر خنک کننده و برش
لوله ها پس از خروج از srm بر روی بستر خنک کننده جهت عملیات نرماله کردن قرار میگیرند و توسط اره های سرد بر به اندازه طول سفارش بریده میشود
عملیات پرداخت نهایی
بر روی لوله های تولید شده پرداخت لبه های دو سر لوله ، تست هیدروستاتیک و غیر مخرب (ٍEDDY CURR_UT-FLUX LEAKAGE) و بازرسی چشمی ، انجام میشود و در نهایت لوله ها جهت عرضه به بازار بصورت شش گوش بسته بندی میگردند
تولید لوله اینچ
ظراحی اولیه کارخانه لوله سازس گروه ملی صنعتی فولاد ایران جهت تولید لوله
اینچ تا اینچ بوده و از آنجاییکه یکی از پر مصرف ترین لوله ها در صنعت نفت لوله بیدذز سایز اینچ با قطر خارجی 168/3 میلیمتراست بنابراین نیاز به این سایز مارا به آن داشت که امکان سنجی تولید آن را در دستور کار قرار داده و به همین منظور مطالعه و تحقیق بر روی فرایند شروع شد ابتدا با استفاده از مهندسی معکوس توانستیم اطلاعات و اندازه های نهایی کالیبر و قطرسنبه ها را بدست اوریم مراحل مهم و عمده طراحی اول چگونگی تولید لوپه مناسب درپرس و دوم کالیبراسسیون غلتکهای شلیک و غلتکهای SRM بود
برای تولید لوله 6 اینچ دو پیشنهاد مطرح گردید
- استفاده از بلوم با مقطع 225 * 225 ( در نتیجه تغییر ابعاد حوضچه فعلی پرس )
- استفاده از بلوم معمولی خط یعنی بلوم 200 * 200
پیشنهاد اول بدلیل نیروی سوراخکاری کمتر دارای مزیت است و از جهت تغییر در حوضچه و همچنین شکل تامین مواد اولیه آن در چالش قرار میگیرد اما در پیشنهاد دوم مهمترین نگرانی و دغدغه افزایش نیروی سوراخکاری بعات افزایش طول لوپه در هنگام سوراخکاری است محاسبات تئوری فشار لازم برای سوراخکاری در حالت دوم 180 بار را نشان میداد در حالیکه فشار نرمال خط حدود 140 بار است
هر پیشنهاد مورد آزمایش قرار گرفتند و خوشبختانه در آزمایش پیشنهاد دوم عملیات سوراخکاری با سرعت مناسب و با فشار 170 بار انجام گردید بنابراین راه حل دوم تصویب گردید و مرحله طراحی و کالیبراسیون غلطک های شلیک و کشش آغاز گردید
اصولا یک کالیبر در نورد بروش میز شلیک مطابق شکل پایین می باشد که همانطوریکه مشخص است دارای یک شعاع بزرگ و یک شعاع کوچک است هر چه اختلاف بین این دو شعاع کوچکتر باد اختلاف ضخامت لوله کمتر میشود و مطلوبیت محصول افزایش میابد