فرایندهای ساخت لوله
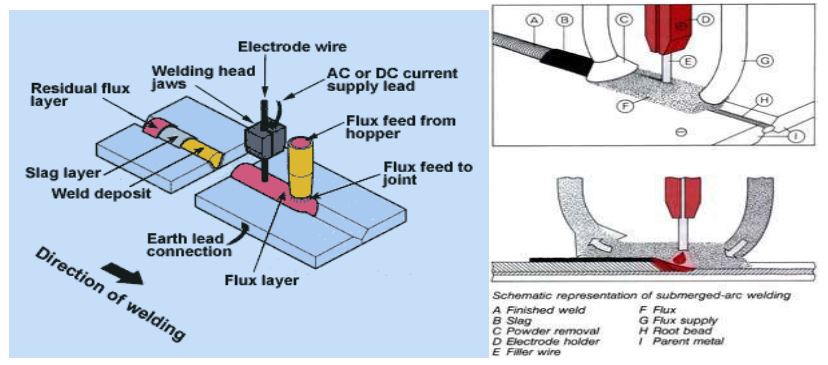
فرایندهای ساخت لوله
فرایند ساخت لوله , روشهای ساخت و تولید لوله به دو دستۀ کلی تقسیم میشوند: روشهای بـدون درز و روشـهای تولیـد لــوله بـا جوشـکاری. در
روشهای تولید لولۀ درزدار از ورق کارگرم شده استفاده میشود. ورق باید به شـکل لولـه در آمـده و درز آن جوشـکاری شـود.
فرایندهای شکل دهی ورق مورد استفاده در ساخت لوله عبارتند از
- شکلدهی سه غلتکی
- شکل دهی ورق به شکل U&
- شکلدهی ورق به شکل J
- شکل دهی اسپیرال
روشهای جوشکاری لوله به دو دستۀ بااستفاده از فلز پرکننده و بدون استفاده از فلز پرکننده تقسیم بندی می شود روشـهای
جوشکاری با فلز پرکننده عبارتند از
- جوشکاری زیرپودری
- جوشکاری GMAWوزیر پودری
جوشکاری زیرپودری
جوشکاری به روش زیر پودری یکی از روشهای جوشکاری قوسی برای تولید لوله است. در این روش، بـرخلاف سـایر روشـهای قوسی، قوس زیر فلاکس پنهان میباشد. یکی از ویژگیهای این روش نرخ رسوب بـالا مـیباشـد. جریـان الکتریکـی حاصـل از ژنراتور، ترانسفورماتورـ یکسوکننده و یا ترانسفورماتور از طریق نازل راهنما و سیم الکترود به قوس و قطعۀ کار هدایت میشود
حرارت حاصل از قوس ، موضع جوش و پودر جوش را ذوب کرده و حوضچۀ بوجود میآید. در انواع این فرایند، دستگاه جـوش بـــــــــــه طـــــــــــور خودکـــــــــــار و مـــــــــــداوم ســـــــــــیم الکتـــــــــــرود را از میـــــــــــان نازل راهنما و لایۀ پودر عبور داده و به طرف حوضچۀ جوش هدایت میکند که پس از ذوب، در سرتاسر محـل اتـصال رسـوب
داده میشود
پودر جوشکاری پیشاپیش قوس، ریخته شده و پس از جوشکاری و انجماد جوش، قسمتی از آن که ذوب نشده توسط دسـتگاه مکنده جمع میشود و بخشی از آن که ذوب شده، به صورت قشر شیشهای )شلاکه( بر روی جوش باقی مـیمانـد کـه از روی جوش جدا میشوددر این فرایند، از مفتول بدون روکش استفاده شده و برای حفاظت حوضچۀ جوش از فلاکس دانهبندی شده استفاده میشود. بنابرین قوس کاملاً مخفی بوده و براین اساس از آمپرهای خیلی زیاد، بدون هیچگونه پاشش و حـبس هـوایی میتوان استفاده نمود. به دلیل آمپر بالا میزان نفوذ در یک پاس و نرخ رسوب فلز جوش در این روش بالاست
جوشکاریGM
دردستگاه ابتدایی GMAWسیم از یک لولۀ با انعطاف به مشعل هدایت شده و جریان الکتریکی توسط اتصال کننده بـه سـیم متصل میشود.گاز محافظ از نازل عبور کرده و اطراف سیم را احاطه میکنـد. بـه ایـن ترتیـب نـوک سـیم و حوضـچۀ جـوش محافظت میشود.انتهای الکترود توسط حرارت قوس و مقاومت الکتریکـی سـیم ذوب شـده و قطـرات مـذاب در اثـر نیـروی دینامیکی، مغناطیسی و جریان گاز جدا شده، سرتاسر قوس را طی کـرده و بطـرف حوضـچۀ جـوش سـقوط مـیکنـداز روش GMAWبرای پاس ریشۀ لوله استفاده میشود. پاس ریشه پشت بند پاسهای بعد که با زیرپودری داده می شوند، اسـت بـرای جوشکاری فولادهای ساختمانی از گاز کربنیک، مخلوط کربنیک و آرگون، آرگون و اکسیژن استفاده میشود. از آرگون خـالص برای جوشکاری فولادها استفاده نمیشود زیرا باعث نا آرامی قوس و بوجود آمدن عیب در جوش میشود در مگ بجای آرگون از گاز کربنیک که گازی فعال است، استفاده میشود. حرارتی که این گاز ایجاد میکند و سرعت جوشـکاری بالاسـت و قیمـت آن نسبت به گاز خنثی کمتر است، ولی یک عیب عمدۀ آن نا آرامی قوس و پاشش فلز جوش است
مزایای فرایند GMAWعبارتند از:حذف سرباره و عدم نیاز به پاک کردن فلاکس قابلیت اتوماتیک شدن نیاز کـم بـه مهـارت اپراتورتنها روشی است که روی تمام آلیاژها میتوان آنرا پیاده کردنقطۀ شروع و توقف جوشکاری با این روش کم است
روشهای تولید لوله های درزدار
یکی از روشهای قدیمی تولید لوله، روش U&Oاست. در این روش، بوسیلۀ قالبهایی ابتدا ورق را بـه شـکل Uو سـپس Oدر می آورند. شکل دهی ورق در حالت سرد انجام میشود. قبل از شکل دهی، لبههای ورق پخ زده میشوند و بعد از شکل دهـی، به صورت درز مستقیم جوشکاری میشودلبههای درز لوله به هم فشرده شده و در ایستگاه پاس ریـشه بـا روش GMAWبـه هم جوش میشوند. سرعت جوشکاری در مرحله بسته به ضخامت ورق، بـین 5تـا 12متـر بـر دقیقـه اسـت.بعـد از ایـستگاه GMAWلوله به ایستگاه جوش زیرپودری منتقل میشود. در ایستگاه جوش زیرپودری ابتدا پاس داخل و سپس پـاس خـارج اعمال میشود. در پاس داخلی و خارجی لوله متحرک بوده و دستگاه جـوش ثابـت، در پـاس داخلـی دسـتگاه جـوش توسـط بازوهای متحرکی به داخل لوله رفته و جوشکاری را انجام میدهد. پرواضح است که پاس خارجی بعد از سرد شدن کامل پاس داخلی اعمال میشود
تولید لولۀ اسپیرال
تولید لوله به روش اسپیرال یکی دیگر از روشهای استاندار تولید لوله در جهان است. در این روش، ورق با گذشتن از یک سری غلتکها با درزی حلزونی) اسپیرال( به شکل لوله در خواهد آمد. برخلاف لولۀ درز مستقیم که قطر لوله بستگی بـه پهنـای ورق داشت، در این روش قطر لوله با تغییر زاویۀ تغذیۀ اولیۀ ورق تغییر خواهد نمود. با تغییر زاویۀ تغذیه، لوله با قطرهـای مختلـف میتوان تولید کرد، در حالیکه در روش درز مستقیم باید کل قالبهای خط تولید باید تعویض شوند. از اینرو در روش اسـپیرال،لوله با قطرهای مختلف را میتوان با هزینۀ کمتری نسبت به درز مـستقیم تولیـد کـرد.لولـههـای اسـپیرال بـه دو روش یـک مرحلهای ودو مرحلهای تولید میشوند
لولۀ اسپیرال یک مرحله ای
این روش یکی از متداولترین روشهای تولید لوله در جهان و شکل اولیۀ تولید لولۀ اسپیرال است. مراحل تولیـد در ایـن ر وش عبارتند ازآماده سازی ورق، شکل دهی ورق و جوشکاری زیرپودری داخل و خارج. در مرحلۀ آماده سازی ورق، سر ورقها به یکدیگر جوش داده می شوند و لبۀ ورق پـخ زده شـده و ورق صـاف مـیشـود. اگـر عملیات شکل دهی را کامل انجام دهند باید لبۀ ورق پیش خـم شـود تـا از ایجـاد برآمـدگیهای غیـر قابـل پـرس جلـوگیری
شود.برای جوشکاری درز اسپیرال، ابتدا درز داخلی در موقعیت ساعت 6توسط دستگاه جوش زیرپـودری جـوش داده خواهـد شد. پاس خارجی در موقعیت ساعت 12جوش داده خواهد شد. تنظـیم مـشعل جوشـکاری )(Welding headبـرروی درز بـه صورت اتوماتیک انجام می گیرد. پس از جوشکاری درز، لوله برش خورده و به مراحل بعدی منتقل خواهد شد.سرعت تولید در این روش، توسط سرعت جوشکاری زیرپودری تعیین میشود. سرعت جوشکاری زیرپودری در حدود 1الی 2/5متر بـر دقیقـه است، گاهی تا 3متر بر دقیقه هم میرسد. از آنجایی که سرعت جوشکاری زیرپودری محدود است، سرعت تولید در این روش کند است
لولۀ اسپیرال دو مرحله ای
تولید لولۀ اسپیرال دو مرحلهای مانند روش یک مرحلهای است، با این تفاوت که در این روش در حین شـکل دهـی ورق، درز جوش با GMAWجوشکاری میشود. این جوش پاس ریشه را تشکیل میدهد در مراحل بعدی، درز از داخل و خارج بوسـیلۀ چند دستگاه زیرپودری پر میشود. این فرایندچهار مرحلۀ اساسی دارد:آماده سازی ورق، شـکل دهـی ورق ، جـوش GMAW وجوش زیرپودری داخلی وخارجی
در روش دو مرحلهای علاوه بر راندمان تولید بالا ) به دلیل شکل دهی سریع(، یک مزیت تکنیکی به لحاظ جدا بـودن مرحلـۀ شکل دهی و جوش نهایی از یکدیگر وجود دارددر ایستگاه شکل دهی در حین شکل دهی پای ریـشه بـا روش GMAWداده میشود سرعت این دستگاه با گاز کربنیک در حدود 12متر بر دقیقه است. این جوش در موقعیت ساعت 6ایجاد میشود
دقت ابعادی لوله های روش یک مرحله ای و دو مرحله ای
در تولید لوله اسپیرال دو مرحلهای. ، لولهها با دقت ابعادی زیادی تولید میشوند . سیستمهـای لولـه اسـپیرال دو مرحلـه ای عمدتا“دارای ویژگیها و امکانات زیر میباشند
- راهنمای مرکز ورق و کنترل اتوماتیک
- انجام اتوماتیک اتصال دوکویل جدید وقدیم
- سیستم جمع کنندۀ ورق برای جریان پیوستۀ تولید
- واحد شکل دهی ورق، شامل سیستم خمش سه غلتکی ) (Three-roll Bendingو محفظۀ راهنمای خارجی لوله
- پیش خمش لبههای ورق برای جلوگیری از اثر برگشت فنری
- سیستم کنترل درز اتوماتیک با دقت 0/1 mm
- فرایند جوشکاری GMAWپیوسته با سرعت12
- تنظیم پارامترهای جوشکاری با سرعت تغذیه، بصورت اتوماتیک
این ویژگیهای باعث شده که لوله های تولیدی با این روش از دقت ابعادی بالایی برخوردار باشند.
در کل از نظر دقت ابعادی روش دو مرحلهای دارای مزایای زیر میباشد
- مستقیم بودن لوله st
- تلورانس کم قطر و بیضوی بودن
مقایسۀ خواص جوش لوله در روش دو مرحله ای و یک مرحله ای
در اثر جوشکاری ذوبی حرارت از منبع متحرک وارد فلز شده و سه منطقه در آن بوجود میآورد : فلز جوش، منطقۀ متـأثر از حرارت ) (HAZو فلز پایه
در تولید لوله به روش دو مرحلهای و یک مرحلهای، پارامترهای مؤثر بر خواص فلز جوش، ناحیۀ متـأثر از حـرارت بـا یکـدیگر تفاوت زیادی دارند. این تفاوتها باعث ایجاد اختلاف، بین خواص لولـههـای تولیـد شـده در خـط تولیـد یـک مرحلـهای و دو مرحلهای خواهد شد. برای شناخت این تفاوتها باید عوامل مؤثر بر خواص سه ناحیۀ مذکور و همچنین تفاوتهای موجـود در شرایط جوشکاری لوله در هر دو روش تولید مورد بررسی قرار گیرند.برای جوشکاری درز اتصال اسپیرال از فلز پرکننـده هـای مختلفی استفاده میشود که خواص فلز جوش از یک سو به ترکیب شیمیایی فلـز پرکننـده و از سـوی دیگـر بـه متغییرهـای
فرایند جوشکاری و نوع فرایند آن برمیگردد. در روش یک مرحلهای فقط از روش جوش زیرپودری استفاده میشود در حالیکه در روش دو مرحلهای از دو جوش زیر پودری و GMAWاستفاده میشود.تفاوتهای پارامترهـای جوشـکاری در دو روش، بـر خواص فلز تأثیر میگذارد
تأثیر عناصر بر ریزساختار خواص فلز جوش در روش یک مرحلهای دو مرحله ای
در اسپیرال دومرحلهای، از روش GMAWبا گاز محافظ CO2برای ایجاد پاس ریشه که یکنوع جوش موقت است و مرحلۀ بعد ذوب میگردد.وبرای جوش اصلی از سیم جوش S2Moوپودرلینکلن P223استفاده سده است. روش یک مرحلهای فقط از سیم جوش S2Moوپودرلینکلن P223استفاده شده است. با توجـه بـه نقـش عناصـر در ریزسـاختار و در تنیجـه خـواص مکانیکی و فیزیکی انتظار میرود که این دو جوش بـا یکـدیگر تفـاوت داشـتهباشـند.در جـوش لولـۀ تولیـد شـده بـا روش دو مرحلهای، در اثر امتزاج فلز جوش حاصل از سیم جوش S2MOبا فرایند SAWو SG2با فرایند ، GMAWمیزان منگنـز و
مولیبدن کاهش مییابد و میزان کربن فلز جوش افزایش مییابد. در روش یک مرحلهای میزان کربن آن کمتر و میزان منگنز، و مولیبدن آن بالاتر خواهد بود. تفاوت بین درصد عناصر در فلز جوش باعث ایجاد خواص و ریزساختارها مختلفی خواهد شـد.
مثلاً انتظار میرود که مقاومت به ضربۀ فلز جوش روش دو مرحلهای کمتر از یک مرحلهای باشد، البته مقاومت به ضـربه فقـط به ترکیب شیمیایی فلز جوش بستگی ندارد بلکه عوامل زیادی با هم بر روی آن اثر میگذارند که در مقایسۀ کامل، بایـد آنهـا را نیز در نظر گرفت. یا تغییرات ریزساختار به دلیل تغییر میزان مولیبدن که اثر زیادی بر ریزساختار و اسـتحکام کشـشی فلـز جوش دارد، ایجاد میشود.
ترکیب شیمیایی فلز جوش خالص.
مواد پرکنندۀ مصرفی |
درصد وزنی عناصر فلز جوش خالص | ||
Mo | Mn | Si | C |
0.5 1.33 0.38 0.08 – 0.7-1 0.5-0.8 0.05-0.1 |
P223 با پودرS2Mo CO2 با گاز محافظSG2 |
نقش گازهای محلول بر فلز جوش
در روش دومرحلهای، فلز جوش با دو روش GMAWو SAWایجـاد مـیشـود ولـی در روش تـک مرحلـهای فقـط از SAW استفاده میشود. این تفاوت باعث تغییر کیفیـت جـوش مـیشـود. در جوشـکاری GMAWبـا اسـتفاده از گازمحـافظ ،CO2 اکسیژن و سایر گازهای دیگر جذب فلز جوش میشوند.در هـر صـورت میـزان اکـسیژن فلـز جـوش رسـوب یافتـه بـه روش GMAWکمتر از روش SAWاست. افزایش میزان اکسیژن فلز جوش، باعث کاهش انرژی ضربه و چقرمگی جوش میشود.در روش دومرحلهای برای ایجاد پاس ریشه از روش GMAWاستفاده میشود که اکسیژن کمتری نـسبت بـه روش SAWدارد.
در روش یک مرحلهای تمام درز اتصال بـا روش SAWپـر مـیشـود. در کـل اکـسیژن جـذب شـده بـه فلـز جـوش در روش دومرحلهای کمتر از روش یکمرحلهای است و انتظار میرود که میزان مقاومت به ضربۀ فلز جوش لولههـای تولیـدی در خـط تولید دومرحلهای، در شرایط برابر بیشتر از مقاومت به ضربۀ جوش لولههای تولید شـده در خـط یـک مرحلـهای باشـد. البتـه امکان دارد این اثر ناچیز باشد. میزان تفاوت به حجم فلز جوش رسوب یافته به روش GMAWبـستگی دارد. افـزایش میـزان اکسیژن باعث کاهش فریت سوزنی نیز میشود که مستقیماً بر خواص مکانیکی جوش اثر میگـذارد.در روش ،GMAWعـلاوه بـــــر اکـــــسیژن، میـــــزان هیـــــدروژن جـــــذب شـــــده بـــــه فلـــــز جـــــوش خیلـــــی کمتـــــر از روش SAWاست. بنابر این در جوشهای لولههای تولیدی در خط دو مرحلهای، با توجـه بـه اینکـه بخـشی از درز اتـصال بـا روش GMAWپر میشود، انتظار میرود که میزان هیدروژن کمتر از جوشهای ایجاد شده در خط یک مرحلهای باشـد. هیـدروژن میزان تنش لازم برای جوانهزنی ترک را کاهش میدهد و باعث تسریع جوانهزنی و رشد ترک میشود. البته مطـابق اسـتاندارد ،API5Lدر اسپیرال دو مرحلهای، پاس ریشه باید کاملاً ذوب شود، با این وجود باز هم میزان هیدروژن در این حالت کمتـر از مقدار هیدروژن جوشی خواهد بود که تماماً با روش SAWپر شده است. بنابراین انتظـار مـیرود، لولـههـایی کـه در خـط دو
مرحلهای تولید شدهاند، مقاومت به ترک هیدروژنی بیشتری نسبت به روش یک مرحلهای داشته باشند
اثر متغیرهای فرایند جوشکاری بر خواص فلز جوش
متغیرهای فرایند جوشکاری برخواص مکانیکی ریزساختار و خواص متالورژیکی فلز جوش تاثیر دارد. در این قسمت از گـزارش به اثر، متغیرهای فرایند بر فلز جوشهای پرداخته میشود در روش دو مرحلهای از جریان کمتری برای پـر کـردن درز اتـصال استفاده ی شود. با جریان کم حرارت کمتر به فلز جوش و فلز پایه وارد می شود. حـرارت کـم باعـث کـاهش دمـای پیـشگرم پاس جوش خارجی است که در موقعیت ساعت ،12در خارج از لوله ایجاد می شود. این حرارت را میتـوان بـه عنـوان دمـای بین پاسی در نظر گرفت. دمای بین پاسی یکی از متغیرهای مهم فرایند، میباشد. دمای بین پاسی یعنی دمای جوش درسـت بلافاصله بعد از هر پاس. در جوشهای چند پاسه این عامل بسیار مهم است. در یک بررسی بـر روی الکتـرود بـا 0/03درصـد
کربن و 0/6درصد منگنز، مشاهده شد که با تغییر دمای بین پاسی از 20درجهسانتیگراد به 300درجهسـانتیگراد، سـختی از 197ویکرز به 155ویکرز کاهش مییابد
مشاهدات متالوگرافی نیز نشان دادند که با افزایش دمای بین پاسی تغییر زیادی در ریزساختار و درشت ساختار ایجاد میشود. با افزایش دمای بین پاسی نسبت ساختار ستونی فلز جوش به صورت فریت اولیه کاهش و ساختار ریز دانه افزایش مییابد.
. دمای بین پاسی بر خواص جوش تأثیر دارد. برای جوشکاری لولههای نفت و گاز که انرژی ضربه مهم است رعایت دمای بـین پاسی مناسب ضروری میباشد. بنابراین با توجه به بالابودن جریان در روش یک مرحلهای دمای بـین پاسـی بـالاتر از روش دو مرحلهای بوده وبر اساس اطلاعات اولیه، انتظار میرود که میزان مقاومت به ضربۀ فلـز جـوش در روش دو مرحلـهای کمتـر از روش یک مرحلهای باشد، ولی همانطور که گفته شد برای نظر قطعی باید سایر عوامل نیز در نظر گرفته شود. ولی تفاوت بـین دمای بین پاسی برای دو روش تولید لوله وجود دارد. میزان اثر آن به عوامل دیگر بستگی دارد
اثر پارامترهای جوشکاری بر HAZدر روش یک مرحلهای و دو مرحله ای
در تولید لولۀ اسپیرال به روش دو مرحلهای و یک مرحلهای، سرعت سرد شدن جوش، میزان حرارت ورودی تفاوت دارند کـه اثر آن بر فلز جوش مورد بررسی قرار گرفت. در این بخش بـه میـزان و نحـوۀ تـأثیر آن بـر ناحیـۀ متـĤثر از حـرارت پرداختـه میشود.در یک فرایند هر اندازه سرعت کندتر و جریان بیشتر شود حرارت ورودی بیشتر خواهد شد. حرارت ورودی زیاد باعث درشت دانگی در HAZمیشود. در اسپیرال یک مرحلهای، سرعت جوشکاری کندتر از دو مرحلهای می باشد. اصولاً باید جریان، برای رسـیدن بـه نفـوذ کامـل افزایش یابد. در نتیجه حرارت بیشتری به فلز پایه وارد میشود. در تولید لوله به روش اسپیرال دو مرحلـهای، بـه دلیـل اینکـه پاس اول به روش GMAWایجاد شده از آنجایی که نفوذ به دلیل وجود پاس ریشه کمتر از روش یک مرحلهای است نیـاز بـه جریان زیادی هم نیست. بنابراین در این روش حرارت کمتری به ورق لوله وارد شده و پیشبینی میشـود کـه ناحیـۀ اطـراف
جوش در لولههایی که به این روش تولید شدهاند تاثیر کمتری نسبت به روش قبل، از حرارت ببینند.
به طور کلی هر قدر سرعت سرد شدن زیادتر باشد، فازی که تشکیل میشود سختتر خواهد بود.در اثر جوشـکاری دمـای فلـز اطراف جوش به دمای آستنیته میرسد. دمای ناحیۀ متاثر از حرارت HAZدر جوشکاری به حدود 1150درجـه سـانتیگـراد میرسد. این دما کمی از دمای آستنیته کردن معمولی بیشتر است. و دانه های آستنیت درشتتـری ایجـاد مـیکنـد.حـرارت ورودی زیاد باعث درشت دانگی نیز میشود.در تولید لوله به روش جوشکاری اسپیرال یـک مرحلـهای، ابتـدا و انتهـای لولـه و وسط لوله وضعیت ثابت دارند. چون بعد از جوشکاری لوله بریده میشود. بنابراین سرعت خنک شدن ناحیـۀ متـاثر از حـرارت و جوش در کل لوله یکسان است. به علت اینکه سرعت خنک شدن ناحیه متاثر از حرارت HAZدر کل طول لوله ثابت بوده انتظار میرود که ناحیه متاثر از حرارت در لولههایی که از این روش تولید شده اند یکنواخت باشد.در تولید لوله بـه روش اسپیرال دو مرحلهای، ابتدا پاس ریشه بصورت خال جوش به روش ، GMAWبا سرعت بـالایی جوشـکاری انجـام مـیشـود و ناحیه متاثر از حرارت باریکی ایجاد میکند. در روش GMAWحرارت ورودی نسبت به روش زیرپودری کم اسـت بـه همـین دلیل، حرارت ناشی از آن، تاثیر کمی برناحیۀ متاثر از حرارت میگذارد. ولی سرعت خنک شدن آن بالاست، چـون جوشـکاری به سرعت انجام میشود. در این فرایند هم دمای ماکزیم منطقۀ متاثر ازحرارت به دمای آستنیته می رسد و بعد از سریع سـرد
شدن، در ناحیۀ متاثر از حرارت HAZساختارهای سختتر مانند فریت سوزنی یـا بینیـت تـشکیل مـیشـود. فولادهـای API
معمولاً کربن کمی دارند و درصد، مارتنزیت کمی تشکیل میشود.
در مرحلۀ بعد، جوشکاری در ایستگاه زیرپودری انجام میشود. حرارت ورودی در فرایند زیرپـودری بیـشتر از GMAWاسـت. حرارت این مرحله باعث تمپر شدن منطقه متاثر از حرارت ) (HAZمرحلۀ اول شده و عملاً باعث میشود که سـاختار تـشکیل شده در منطقه متاثر از حرارت ) (HAZلوله با روش قبل )جوشکاری اسپیرال یک مرحلهای( تفاوت عمـدهای داشـته باشـد، از بریده شدن به طولهای استاندارد، جوشکاری زیرپودری روی آن انجام میشوددر جوش دو مرحله ای منطقه متاثر از حـرارت )، (HAZجوش در ابتدا، انتها و وسط لوله با یکدیگر فرق میکند. سرعت سرد شدن بر خواص مکـانیکی و ریزسـاختار منطقـه متاثر از حرارت ) (HAZتاثیر میگذارد و در نتیجه آن، عدم یکنواختی در ریزساختار و خواص مکانیکی لوله در ابتدا و انتهـا و
وسط لوله روبرو خواهیم بود
تنش پسماند و اعوجاج دو لوله ها
تنش پسماند، تنشی است که در صورت برداشتن تمام نیروهای خارجی در جسم باقی میماند. تغییرات غیر یکنواخت دمـایی
باعث ایجاد تنش پسماند میشوندیکی از راههای کاهش تابیدگی استفاده از خال جـوش اسـت. ایجـاد خـال جـوش در طـول
اتصال قبل از پر کردن اتصال اثر زیادی بر تابیدگی میگذارددر تولید لوله به روش دومرحلهای، از دو پاس برای پر کـردن درز
اتصال استفاده میشود، بنابراین انتظار میرود که میزان اعوجاج و تنش پسماند در این روش کمتر از روش یک مرحلهای باشد
که حجم جوش بیشتری در یک پاس رسوب داده میشود
مزایای روش دو مرحله ای عبارتند از:
- بهرهوری روش دو مرحلهای به علت سرعت تولید بـالا ناشـی از اسـتفاده از ،GMAWبـالاتر از روش یـک مرحلـهای
است.)تقریبا” پنج برابر - در حجم تولید مشابه،سرمایه گذاری لازم برای جوش یک مرحله ای بالاتر خواهد بود
- خواص مکانیکی جوش روش دو مرحلهای به دلیل استفاده از روش GMAWدر پاس ریشه و کم بـودن میـزان گـاز
حل شده در این جوش، بهتر از روش یک مرحلهای است
- تغییرات قطر در ابتدا و انتها ی لولههای تولید شده به روش دو مرحلهای کمتر از یک مرحلهای است
- میزان انحراف در طول لوله درلولههای تولید شده به روش دو مرحلهای کمتر از یک مرحلهای است
- دقت ابعادی در روش دومرحلهای بالاتر از یک مرحلهای است
- در روش دو مرحلهای خطاها و عیوب در شکل دهی ورق مستقیماً وارد جوش اصلی نمیشود و در صورت بروز عیـوب
تعمیر آن آسانتر از روش یک مرحلهای است، و جوش اصلی بدون عیب خواهد بود - میزان اعوجاج و تنش پسماند در لولههای روش دو مرحلهای کمتر از یک مرحله ای است
- مقاومت به خوردگی لولههای روش دومرحلهای به دلیل تنش پسماند کمتر، نـسبت بـه روش یـک مرحلـه ای، بـالاتر
است - انجـام جـوش اصـلی)(SAWدر روش دو مرحلـه ای در حـالتی صـورت مـی گیردکـه لبـه هـای ورق توسـط جـوش
)(GMAWقبلا” ثابت شده اند بر خلاف جوش یک مرحله ای که جوش در حالت حرکت لبه ها صورت می گیرد - انجـام جـوش اصـلی)(SAWدر روش دو مرحلـه ای در حـالتی صـورت مـی گیردکـه لبـه هـای ورق توسـط جـوش
)(GMAWقبلا” ثابت شده اند بر خلاف جوش یک مرحله ای که جوش در حالت حرکت لبه ها صورت می گیرد
با تمام مزایایی که روش دو مرحلهای دارد دارای معایبی نیز می باشد که عبارتنداز
- کاهش میزان عناصر آلیاژی مطلوب در فلز جوش S2Moبا روش SAWبه دلیل امتزاج با فلـز جـوش SG2در پـاس
ریشه و کاهش خواص کششی فلز جوش خالص - عدم یکنواختی جوش در ابتدا و انتهای لوله و ایجاد عیوبی چون مک در این مناطق
- عدم یکنواختی سرعت سرد شدن در ابتدا و انتهای لوله و عدم یکنواختی خواص ناحیۀ کنار جوش
- پیچیدگی تنظیمات وتولید در روش دو مرحله ای بیشتر می باشد
- نیاز به فضای تولید بیشتری نسبت به یک مرحلهای دارد)در صورت حجم تولید مشابه فضای تولید کمتر می باشد
مزایای روش تک مرحلهای عبارتند از
- عدم وجود ابتدا و انتهای درز جوش و عیوب مربوط به آن
- نیاز به تجهیزات وفضای تولیدی کمتر
- چقرمگی جوش به دلیل دمای بین پاسی بالاتر از دمای بین پاسی روش دو مرحلهای
- با توجه به حجم کمتر تجهیزات مورد نیاز ،عموما“قابل حمل و نصب در نزدیکی سات لوله کذاری می باشد
معایب این روش عبارتند از
- سرعت تولید پایین
- پایین بودن کیفیت جوش نسبت به روش دو مرحلهای به دلیل زیاد بودن گازهای محلول در جوش
- زیاد پودن تنش پسماند نسبت به روش دو مرحلهای به دلیل حرارت ورودی بالا
- کم بودن مقاومت به خوردگی H2Sو SCCبه دلیل تنش پسماند بیشتر نسبت به روش دو مرحله ای
- جوانه زنی و رشد ترک هیدروژنی در لولههای یک مرحلهای بالاتر از دو مرحلهای است چون میزان هیـدروژن محلـول
در فلز جوش آن بیشتر است - پایین بودن دقت ابعادی در مقایسه با روش دو مرحله ای
- بالا بودن مشکلات نسب لوله در خط لوله به دلیل تغییرات قطر بیشتر نسب به روش یک مرحله ای
- القای عیوب و مشکلات مرحلۀ شکل دهی ورق به جوش اصلی
- انجام جوش SAWدر حالتی که لبه های اتصال نسبت به یکدیگر درحالت حرکت می باشد