ذوب در كوره كوپل
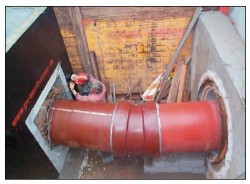
ذوب در كوره كوپل
كوره كوپل از تجهيزات معمول ذوب است كه در ريخته گري وجود دارد .يك كوره عمودي استوانه اي شكل است كه از بالاي آن قراضه فولادی , برگشتي چدن , مواد چرخه فرايند به عنوان ماده خام و كك به عنوان ماده سوختني ريخته مي شود . از پايين هواي گرم شده دميده مي شود كه با آن كك سوخته مي شود . به علت گرماي حاصله افزودني هاي فلزي ذوب مي شوند در در بخش پاييني استوانه Pc ١٤٥٠ در يك 0 ذوب آهن جمع مي گردد .آهن مذاب به صورت پيوسته با درجه حرارت P كانال جمع مي گردد و سپس مخلوط شده و از آن آهن قابل شارژ برداشته مي شود و گوگرد زدايي صورت مي گيرد .
فرايند صورت گرفته در كوره كوپل با محيط زيست سازگار است و نيز مي تواند از صد در صد قراضه استفاده كند .كوره كوپل مي تواند از قراضه هاي پرسي اتو مبيل به صورت زنگ زده و با پوشش و لوله هاي ضايعاتي خارج شده از خطوط داخل زمين استفاده كند بدون آنكه مشكلي داشته باشد و مواد آلوده همرا ه آنها سوخته و وارد معادله انرژي مي شوند . زينك كه پوشش رايج مورد استفاده امروزي است به اكسيد روي تبديل شده و سوخته مي شد كه همراه با ديگر ناخالصي هاي موجود در گازهاي توليدي فيلتر مي شود. ككي كه در اين كوره ها توليد مي شود داراي مقدار كمي گوگرد مي باشد كه در آهن حل مي شود و بر خواص مكانيكي چدن تاثير منفي نمي گذارد .در صورت بالاتر رفتن گوگرد عمليات گوگرد زدايي به كمك ماده مناسب به عنوان مثال كاربيد كلسيم صورت مي گيرد كه گوگرد را به صورت شيميايي جذب مي كند و محصول واكنش به صورت شلاكه بر سطح آهن مذاب شناور مي شود كه قابل زدايش است .
الكتريكي كوره ٣-١-٣ اين كوره نيز از تجهيزات معمول ذوب است كه در ريخته گري وجود دارد . سيستم آن به صورت القاي جريان الكتريكي بوده و نسوز آن به صورت سيلندري شكل درون يك استوانه قرار گرفته است كه دور آن يك سيم پيچ است كه جريان متناوب از آن عبور مي كند لذا در هسته آن كه شامل شارژ فلزي است يك جريان ثانويه القائ مي شود و فقط اين شارژ فلزي تحت تاثير قرار مي گيرد.
در اين روش ديگر توليد كننده ها انرژي مانند كك مورد استفاده قرار نمي گيرند .در مقايسه با كوره كوپل نياز به انرژي و در جه حرارت كمتري داشته و سريعتر مي باشد .
٣-٢ افزايش منيزيم (فرايند نشكن سازي ) در كوره بلند يا كوره كوپل ذوب حاصله چدن بدون عمليات اضافي داراي ساختار گرافيتي عمدتا به صورت ورقه اي است اما آنچه مورد نياز است ساختار گرافيت
كروي معمول است كه در چدن نشكن وجود دارد .اين نياز به وسيله افزودن منيزيم برآورده مي شود .در اينجا عامل مهم ميل تركيبي بالاي منيزيم با اكسيژن و گوگرد است . منيزيم تقريبا تمام اكسيژن موجود در ذوب را كاهش مي دهد و گوگرد را به صورت سولفيد منيزيم در مي آورد .اكسيد منيزيم سبك بوده و همراه با مقاديري سولفيد منيزيم در سطح ذوب قرار مي گيرد و به صورت شلاكه خارج مي شود . با توجه به تحقيقات صورت گرفته هنوز مشخص نيست كه كدام مكانيزم با افزودن منيزيم سبب ايجاد ساختار گرافيت كروي مي شود .به صورت مرجح اين مدل مطرح است كه هنگام گوگرد زدايي تا مقدار ppm حد تنش سطحي بين نطفه هاي خود ساخته گرافيت با سطح ذوب كاهش مي يابد به صورتيكه كريستال هاي گرافيت با به رشد با شكل كروي به علت تنش سطحي كمتر تمايل پيدا مي كنند .
جهت عمليات با منيزيم روش هاي مختلفي وجود دارد به عنوان مثال منيزيم خالص و يا آلياژي در روش ساندويچي كه زير پوشش سراميكي در كف بوته قرار مي گيرند هنگام ريخته شدن مذاب در كف پاتيل فشار بخار لازم را ايجاد مي كنند و يا اينكه منيزيم در روش كنورتور پوشش دار هنگام داخل شدن ذوب مصرف مي شود . يك امكان ديگر افزودن منيزيم به در سيم هاي پر شونده است. (كرد واير ) هم چنين در توليد اتصالات كه به روش ريخته گري در ماسه صورت مي گيرد منيزيم هنگام ريخته گري به روش درون قالب (MOLD IN (مصرف مي شود . در كليه روش هايي كه در بالا ذكر شد منيزيم در ذوب بخار مي شود كه سبب همش آن گشته و با گوگرد و اكسيژن به حالت تعادل در مي آيد و مقادير اندكي از آن به صورت منيزيم باقيمانده در ذوب حل مي شود . ٣-٣ فرايند ريخته گري ٣-٣-١ توليد لوله با روش ريخته گري گريز از مركز
توليد لوله با روش ريخته گري گريز از مركز در قالب فلزي حق امتياز
مهندس آ .ك هاردت است كه در ژانويه سال ١٨٠٩ ثبت شده است اما از اين يافته در آن زمان استفاده نگرديد چون مقدمان فني آن هنوز مهيا نشده بود . از جمله اين مشكلات چگونگي اختصاص ذوب مايع به حركت افقي در قالب در حال چرخش بود . در سال ١٩١٠ اتو برايدز بن راث ماشين ريخته گري متحرك را اختراع كرد .او ايده خود را از يك برزيلي به نام دولاوو گرفته بود كه امروزه در سر تا سر به روش دو لاوا معروف است . ريخته گري گريز از مركز در آلمان اولين با ر در سال ١٩٢٦ صورت گرفت . دو روش كلي در اين فرايند وجود دارد : –1 ( ريخته گري در قالب فلزي (كوكيل )مطابق روش دو لاوو(شكل ٣-٢ ( –٢ (ريخته گري در قالب فلزي (كوكيل )پس از اسپري شدن سطح قالب با پوشان مرطوب
شكل ٣-٢ ريخته گری گريز از مركز در قالب فلزی به روش دو لاوو
در هردوي اين روش ها شكل خارجي لوله به وسيله يك قالب فلزي(كوكيل ) ايجاد مي شود .قالب بر روي محل هاي استقرار تعبيه شده درون دستگاه قرار مي گيرد كه به صورت غلتكي بوده و غلتك ها بالايي بر روي قالب نيرو وارد مي كنند .
در روش اول از آب جهت خنك شدن قالب استفاده مي گردد .نيروي رانشي يك الكتروموتور سبب حركت چرخشي قالب مي گردد . براي ايجاد فضاي سر كاسه لوله از ماهيچه سر لوله استفاده مي شود كه از ماسه و چسب توليد شده است كه در سر قالب قرار مي گيرد . ماشين ريخته گري داراي شيب به سمت سر كاسه لوله است و حركت طولي روي ريل هاي زيرين دارد .در ابتداي اسپيگات (سمت ديگر دستگاه ) تجهيزات تخصيص ذوب قرار دارد كه ذوب براي ريخته گري يك يا چند لوله در آن موجود است. (بارريز) . به وسيله تنظيم سرعت تخليه بارريز مقدار ثابتي از ذوب در واحد زمان وارد قسمت پهن ناوداني هنگام ريخته گري مي شود .
در ابتداي ريخته گري دستگاه به سمت بارريز حركت مي كند و تقريبا ناوداني تا انتها داخل قالب وارد مي شود .قبل از جريان يافتن ذوب قالب حركت چرخشي خود را آغاز مي كند .ذوب ريخته شده در قالب ابتدا فضاي مابين قالب و ماهيچه تعبيه شده را پر كرده و سپس به تدريج در اثر حركت طولي دستگاه كه از بارريز دور مي شود سر تا سر قالب را در بر مي گيرد .ذوب كه تحت اثر نيروي چرخشي قرار دارد به ديواره قالب مي چسبد و شكل يك لوله را در حالت ذوب مي گيرد .با تغيير مقدار ذوب در هنگام ريخته گري و نيز سرعت حركت طولي دستگاه از لحظه شروع پروفيل ضخامت لوله تغيير مي كند. سرعت چرخش با توجه به اندازه اسمي لوله به گونه اي است كه نيروي گريز از مركز ١٥ تا g ٣٠ بر روي ذوب اعمال مي شود.اين نيرو باعث مي شود كه انجماد جهت دار از بدنه قلب به سمت مركز آن صورت گيرد كه به همراه آن تراكم ماده نيز صورت مي گيرد .اين نيرو حتي سبب مي شود كه محصولات اكسيدي ناشي از ذوب به هنگام ريخته گري از آن جدا شده و به سمت سطح داخلي لوله حركت كنند كه در عمليات تكميلي از سطح به راحتي زدوده مي شوند . پس از انجماد و كاهش حجم, لوله توليد شده به راحتي از جداره قالب جدا مي شود.
خروج لوله از سمت سركاسه مي باشد .(شكل ٣-٣)
شكل ٣-٣ خروج لوله از ماشين ريخته گری
٣-٣-٢ ريخته گري در قالب فلزي (كوكيل )مطابق روش دو لاوو در اين روش قالب بدون پوشش است و از خارج توسط آب خنك مي شود . سطح داخلي قالب توسط آج زدن مضرص مي شود .اين شكل مضرص سبب مي شود كه استحكام سطحي افزايش يابد و گيرايي ذوب به قالب در حركت دوراني تامين شود ونيز توزيع پودر جوانه زاي داخل قالب را يكنواخت مي كند لذا لوله چدن نشكن با سطحي عاج دار توليد مي شود . در اين روش زمان تماس ذوب با قالب به علت سرعت سرد شدن بالا بسيار كم است ولوله به راحتي در حداقل زمان جامد شده و از قالب خارج مي شود و بدون وقفه لوله بعدي ريخته مي شود لذا دوام و استحكام قالب حفظ مي شود. ٣-٣-٣ ريخته گري در قالب فلزي (كوكيل )پس از اسپري شدن سطح قالب با پوشان مرطوب هنگاميكه قالب بدون پوشش است سطح داخلي آن در اثر تغيير درجه حرارت دچار تنش مي گردد ولي سطح خارجي داراي نوسانات درجه حرارت كمتري است .
درجه حرارت سطح داخلی تا 0 C1300 می رسد و بین دو مرحله لوله ریزی (ریختن دو شاخه) درجه حرارت سطح داخلی تا 2000c کاهش می یابد. بتوجه به اینکه سطح داخلی قالب سطح خارجی لوله را شکل می دهد کیفیت آن از اهمیت بالایی برخوردار است.در روش اسپری سطح که عمدتا در اندازه اسمی بالای لوله استفاده می شود قالب با پوششی به ضخامت .5mm از بنتونیت و کوارتز محافظت می شود. بوسیله این پوشش نازک دامنه نوسانات درجه حرارت در جداره قالب کاهش پیدا می کند. تجدید این پوشش متناسب با زمان ماندگاری آن است ولی معمولا بعد از هر ریخته گری تجدید می شود.
٣-٣-٤توليد لوله و اتصالات در روش ريخته گري در ماسه روش ريخته گري گريز از مركز براي قطعات متقارن با شكل خارجي سيلندر يا مخروط به كار مي رود .قطعاتي كه داراي انحنا و انشعاب يا چند اتصال هستند (سركاسه اي و يا فلنجي)نياز به روش شكل دهي ديگري دارند . براي ريخته گري قطعات در ماسه به قالبي مطابق شكل خارجي و اجزاي شكل دهنده داخلي (ماهيچه ) نياز است .براي شكل دهي قالب در ماسه از مدل هاي فلزي , چوبي و مواد مصنوعي استفاده مي شود . جنس قالب از ماسه كوارتزي خالص است كه با چسب مخلوط شده است تا مدل بتواند شكل خارجي قطعه را در آن ايجاد كند و در ضمن قادر به تحمل فشار و درجه حرارت مايع ذوب حين ذوب ريزي باشد .قالب ماسه اي بايد بعد از انجماد قطعه به سهولت متلاشي شود و وارد چرخه باز يافت شود.جهت ايجاد شكل داخلي ماسه كوارتزي به صورت تركيب با يك چسب آلي مستحكم مي شود (ماهيچه). ماهيچه نيز پس از انجماد بايد نگهداري خود را از دست داده و متلاشي گردد. شكل ٣-٤ توليد اتصالات را به اين روش نشان مي دهد.
شكل ٣-٤ توليد اتصالات با ماهيچه فدا شونده
٣-٣-٥ توليد لوله در روش ريخته گري در ماسه ريخته گري در ماسه قديمي ترين روش توليد براي ريخته گري لوله و اتصالات است .براي توليد لوله از قالب هاي ماسه اي دو تكه استفاده مي شود و با استفاده از يك ماهيچه قوي بلند سوراخ لوله ايجاد مي شود .در روش هاي پيشرفته تر قالب هاي ماسه اي به صورت عمودي و بدون درز مي باشند .(شكل ٣-٥ )
شكل ٣-٥ اصول ريخته گری لوله به صورت عمودی
a ) سر فدا شونده
b ) تنظيم كننده ذوب ريخته گری چوب
c ) درجه قالب
(d ماسه قالب
e ) ماهيچه استوانه ای
f ) ما هيچه
(g لوله ساخته شده از كاه يا خاك لوله ساخته شده از كاه يا خاك
h) ماهيچه سر كاسه
I) نگهدارنده سركاسه
k) حلقه قفل كننده
مدل شامل سر كاسه و قسمت ميله اي شكل بدنه مي باشد .مدل سر كاسه از پايين به صورت عمودي در درجه قرار گرفته و محكم مي شود .مدل بدنه از بالا هدايت مي شود و توسط يك راهنماي مخروطي شكل در مر كز مدل سركاسه قرار مي گيرد .ماسه قالب در فضاي خالي بين مدل و درجه وارد شده و كوبيده مي شود . جهت افزايش تعداد توليد قالب هاي عمودي بر روي دستگاه چرخنده قرار مي گيرند)(٦-٣ شكل.)
شكل 3-6 سالن ريخته گری قالب هاي عمودی
لوله هاي توليدي مي توانند داراي سركاسه , فلنجي و يا صاف باشند . لوله هاي فلنجي با طول كوتاه عمدتا به صورت قالب دو قسمتي توليد مي شوند . در حالت هاي پيشرفته تر لوله هاي فلنجي توسط جوشكاري و يا پيچ شدن فلنج به لوله هاي توليدي از روش ريخته گري گريز از مركز توليد مي شوند .
٣-٣-٦ توليد اتصالات در روش ريخته گري در ماسه اتصالات در قالب هاي دوقسمتي فداشونده ريخته گري مي شوند .جهت ايجاد شكل داخلي از ماهيچه استفاده مي شود .در تيراژ هاي توليد بالا از ما شين هاي قالب گيري استفاده مي شود .مدل معمولا از فلز و يا پلاستيك ساخته مي شود . ماده قالب به صورت معمول از ماسه كوارتزي و چسب بنتونيت و افزودني خاك زغال است و در درجه توسط لرزش يا پرتاب شدن وفشرده شدن محكم مي شود . در روش هاي پيشرفته ديگر مخلوط رزين مصنوعي همراه با ماسه ماده قالب راتشكيل مي دهند و يا در روش قالبگيري در خلائ استحكام ماسه قالب توسط نيروي فشردگي خلائ و بدون نياز به چسب تامين مي گردد.در خط قالبگيري درجه ها به صورت سري از ماده قالبگيري پرشده و ماده قالب توسط فشار دستگاه فرم اوليه را مي گيرد .مدل آنها از چوب و فلز ساخته مي شوند . در ساخت ماهيچه از ماسه سيليسي و چسب سرد يا گرم استفاده مي شود .
ماهيچه ها بايد آنقدر محكم باشند كه كه فشار استاتيكي ذوب حدود يك بار ٤٠.١ متر را تحمل كنند .در برابر فشار انقباض انجماد نيز مقاوم بوده به صورتيكه هيچ گونه ترك و پارگي ايجاد نشود .در نهايت پس از خنك شدن قطعه به راحتي قابل جداشدن باشند. ٣-٤ عمليات تكميلي كليه مراحل بعدي باقيمانده در فرآيند توليد لوله و اتصالات را در بر مي گيرد كه بعد از ريخته گري لازم اند .